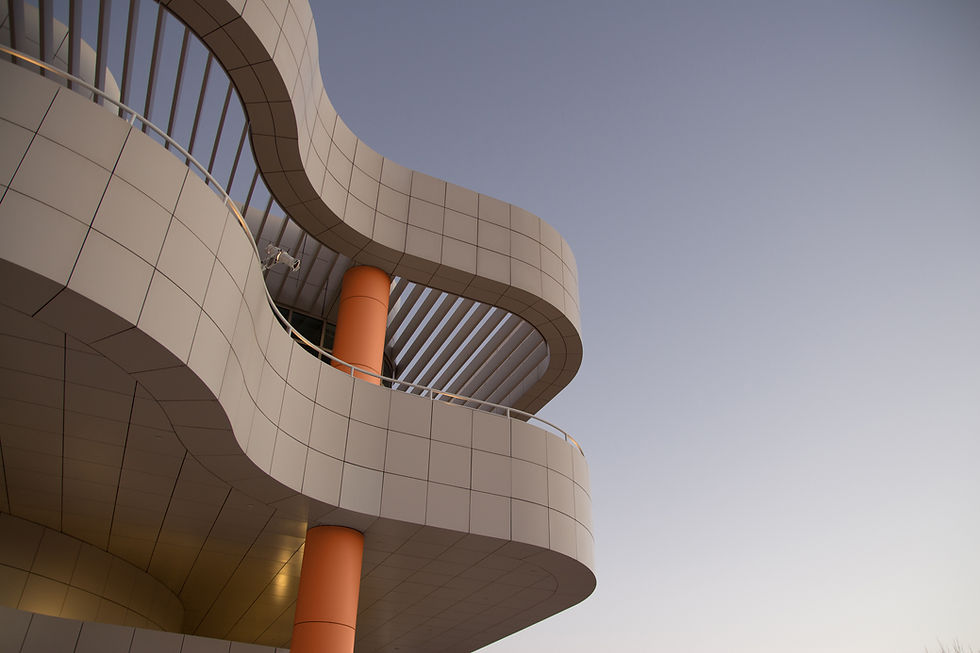
Empowering the Workforce: A Comprehensive Guide to the Connected Worker
Oct 16, 2024
13 min read
0
19
0
Creating a connected workforce is essential for modern organizations seeking to enhance collaboration, efficiency, and safety. By leveraging digital technologies, companies can break down information silos and empower their employees to thrive in a rapidly evolving digital landscape.
This comprehensive guide will explore the concept of the connected worker, the importance of connected worker platforms, and how Syook's Connected Worker Platform can play a pivotal role in this transformation.

Overview of Connected Worker
Digital tools and technologies such as augmented reality (AR), artificial intelligence (AI), the Internet of Things (IoT), and industrial connectivity are revolutionizing how companies connect their workforce with essential knowledge and processes, ultimately enhancing workforce efficiency. The concept of a connected future holds significant implications for various industries.
A new generation of connected workers harnesses these technologies to perform their tasks more effectively and safely, creating less stressful work environments. But who exactly is “the connected worker”? What digital technologies facilitate their connection, and what are they connecting to?
Furthermore, do these digital technologies allow space for workers, whether connected or not? This concept encompasses many facets, some of which have been validated through practical applications in industry, while others remain speculative.
What is a Connected Worker?
A connected worker is an individual who is linked to the people, processes, and products necessary for their daily tasks. Unlike traditional workers who may have to seek out information through physical manuals or by asking colleagues, connected workers have access to all the resources they need via handheld devices or heads-up displays. They not only consume information but also contribute to manufacturing and service systems by sharing their expertise, providing documentation, and offering feedback to improve products and processes.
Connection to People
Connected workers maintain relationships with various individuals, including team members, supervisors, experts, and even customers, through remote collaboration technologies. For instance, augmented reality (AR) allows a remote expert to view what the connected worker sees in real time, guiding them through tasks or decision-making processes. This technology also enables workers to troubleshoot issues with customers remotely, making it more convenient and cost-effective than conducting site visits for straightforward problems.
Connection to Processes
The processes essential for connected workers are accessible through mobile devices and enhanced enterprise collaboration tools. One such tool is a digital mentor that resides on the worker’s smart device. These digital mentors provide instructions and visual guidance based on company procedures and protocols while continuously learning from interactions with human workers using artificial intelligence (AI). Digital mentors are invaluable for training both new hires and experienced employees transitioning to new roles. Beyond onboarding, they serve as an institutional memory, preserving accumulated knowledge and ensuring procedural consistency across various locations.
Connection to Products
Connected workers are also linked to the products they work on. Instead of relying on physical manuals or catalogues, product information is digitally stored on devices that are more convenient for consultation. This data can be viewed through augmented reality, monitored with real-time IoT data, and automated through connectivity solutions. Such resources assist connected workers in navigating products, locating specific items or areas, and addressing common issues in manufacturing and service environments. In summary, connected workers leverage advanced digital technologies to enhance their efficiency and effectiveness in the workplace by connecting seamlessly with people, processes, and products.
What is the Importance of the Connected Worker in the Digital Era?
In the digital age, both executives and customers have grown accustomed to having immediate access to the products and services they desire, often available at a moment's notice or via overnight shipping. However, this expectation places frontline workers—such as manufacturers, assembly engineers, and warehouse staff—in a challenging position. These workers frequently find themselves expected to accomplish today’s tasks at tomorrow’s pace, all while relying on outdated resources.
This oversight may stem from a common perception that the future of work revolves around automation. While certain tasks—especially those that are dangerous, monotonous, or require no specialized skills—have indeed been automated, the technology available today primarily serves to empower workers rather than replace them. For connected workers, the digital era presents a unique opportunity to tackle challenges by providing timely access to the resources they need in the right context.
This access includes information that was previously available only through traditional workflows, often requiring workers to seek out physical references or consult with experts in person. Now, they can receive real-time information instead of waiting for a supervisor to relay it hours or even days later. Furthermore, information that may have been accessible but not immediately actionable can now be visualized effectively through augmented reality, allowing for a more intuitive understanding of data and processes than ever before.
What is a Connected Worker Platform?
A connected worker platform is a comprehensive suite of digital solutions designed to empower frontline workers and service technicians by providing them with digital information and instructions through a mobile-first approach. These platforms utilize digital technologies to connect, automate, and visualize information, thereby enhancing communication, collaboration, and productivity among workers.
This platform acts as a central hub where employees can access real-time information, collaborate with team members, and engage with digital tools to streamline their tasks. By leveraging mobile devices, wearables, and other connected technologies, connected worker platforms ensure that information is readily accessible, enabling workers to perform their duties more efficiently.
The development of connected worker platforms is part of the broader trend of Industry 4.0, which emphasizes the integration of digital technologies into manufacturing and industrial processes. As technology has progressed, organizations have sought ways to enhance the agility and responsiveness of their workforce. This evolution also reflects a shift towards a more mobile and interconnected work environment, recognizing the critical role of real-time data and communication for frontline workers.
Evolution of the Connected Worker Platform
The rise of cloud computing has significantly facilitated the storage and accessibility of large volumes of data generated by connected worker platforms, allowing for seamless integration and analysis. In summary, connected worker platforms have evolved in response to the demands for increased mobility, real-time communication, and data-driven decision-making across various industries. This evolution has been driven by advancements in technology, principles of Industry 4.0, and the widespread adoption of emerging technologies and cloud computing.
The Rise of Mobile Devices
Most frontline workers operate in environments that do not involve traditional desks—whether in the field or on factory floors. A modern workspace provides these workers with access to information via mobile devices rather than relying on desktop stations or paper documentation. Today’s workforce is accustomed to accessing services like banking or travel bookings on their mobile devices and expects similar convenience in their work tools. Manufacturing companies are increasingly equipping their frontline employees with connected mobile tools to ensure high quality and efficiency.
Enabling Connectivity and Integrations
While any company can implement emerging technologies in isolated parts of its operations, using these technologies collectively across operations creates a digital thread throughout the organization. This digital thread links digital twins of processes, facilities, and equipment to their physical counterparts. For many companies, this integrated approach has become standard practice; however, others are still developing their digital thread strategies. As the digital thread becomes more prevalent, it serves as an authoritative source of product data built on CAD and PLM foundations. This ensures that accurate, up-to-date contextual product data is available to empower frontline workers in manufacturing settings.
Digital Work Instructions
Digital work instructions replace traditional paper-based guides with interactive multimedia content accessible on mobile devices such as smartphones, tablets, or smart glasses. These instructions provide frontline workers with step-by-step guidance and real-time information that reduces errors while ensuring compliance with current standards. The multimedia capabilities allow for the integration of images, videos, and 3D models that enhance understanding and make complex tasks easier to navigate. Additionally, interactive elements like checklists engage workers actively while facilitating on-the-job learning. Overall, transitioning to digital work instructions leads to a more adaptable and informed workforce in manufacturing and service industries.
Connected Worker Strategies and Digital Transformation
Connected worker strategies are essential for successful digital transformation within organizations. These strategies require updating processes to align with technological advancements while ensuring seamless integration into existing workflows.
Comprehensive training programs for frontline workers are crucial in helping them navigate new digital tools effectively. Connecting workers with people, products, and processes is fundamental to a successful connected worker approach. This connection breaks down information silos and fosters collaboration across various organizational facets.
Leveraging mobile devices allows frontline workers to access information on the go, enhancing efficiency and responsiveness. By adopting connected worker strategies, companies can create a cohesive ecosystem where information flows seamlessly, empowering their workforce to embrace and contribute to the journey of digital transformation.
Advantages of the Connected Worker Approach
The connected worker approach benefits both employees and forward-thinking companies alike. While developing this approach requires an investment, it pays off significantly in areas such as safety, quality, job satisfaction, and efficiency.
Safety
One of the most significant advantages is that connected workers operate in safer environments compared to traditional workers. Augmented reality (AR) enables hands-free access to critical information while enhancing situational awareness and mobility during emergencies. With AI and IoT technologies providing easy-to-understand indications regarding machine performance issues, connected workers can better comprehend products and processes quickly—potentially reducing workplace accidents. Additionally, connected workplaces benefit from enhanced managerial oversight through improved data access which helps decrease downtime by ensuring smooth operations while maximizing safety.
Efficiency
On an individual level, connected workers demonstrate increased efficiency compared to traditional counterparts due to quicker access to information through mobile devices rather than cumbersome paper references. Remote expert assistance further enhances their autonomy when addressing issues. Automation also plays a role by streamlining routine tasks that do not require specialized skills; AI assistants provide support rather than competition for connected workers’ attention—allowing them more time for tasks that genuinely require their expertise.
Workforce Mobility
Connected workers significantly enhance workforce mobility by utilizing technology for improved communication and collaboration while accessing vital information from anywhere—reducing constraints associated with fixed workspaces. Real-time communication tools foster instant collaboration among team members regardless of location—boosting efficiency while minimizing delays in workflows. This mobility allows connected workers to transition seamlessly between different job sites or locations without losing access to critical information—especially beneficial in industries where employees frequently move between various environments like manufacturing facilities or field service locations.
Job Satisfaction
Safety and efficiency contribute directly toward higher job satisfaction levels among connected workers who possess all necessary resources needed for success within safer environments compared to traditional settings. Providing modern workspaces equipped with state-of-the-art tools reduces employee turnover rates while improving overall job satisfaction—particularly among younger generations accustomed to user-friendly technology experiences outside work contexts.
Increased Collaboration
Connected workers foster collaboration through instant access to shared information along with integrated communication tools that enable real-time teamwork—breaking down geographical barriers while promoting dynamic idea exchanges among dispersed teams. Collaborative features such as video conferencing facilitate seamless communication while centralized repositories ensure everyone has access to up-to-date resources—reducing misunderstandings or errors during projects. These benefits compound as higher job satisfaction reinforces safety measures alongside improved efficiency outcomes leading ultimately toward enhanced productivity levels across organizations employing connected worker strategies successfully.
Key Technologies Driving the Connected Worker
Connected worker platforms leverage a variety of advanced technologies to enhance operational efficiency, safety, and collaboration in industrial settings. Here’s an overview of key technologies that enable connected workers:
Augmented Reality (AR)
Augmented reality superimposes digital information and visuals onto the physical world, making it easier for workers to understand tasks and access critical data. AR can be utilized for maintenance, remote assistance, and training, allowing workers to visualize complex processes and receive real-time guidance from experts. For instance, technicians can use AR to see step-by-step instructions overlaid on machinery, facilitating quicker and more accurate repairs.
Virtual Reality (VR)
Virtual reality creates immersive computer-generated environments that allow employees to engage in virtual training sessions, simulations, and remote collaboration. This technology enables workers to practice skills in a safe environment without the risks associated with real-world operations. For example, VR can be used to simulate emergency scenarios, helping workers prepare for unexpected situations while enhancing their response skills.
Internet of Things (IoT)
The Internet of Things consists of a network of devices, sensors, and software that collect data from both Information Technology (IT) and Operational Technology (OT) systems. IoT can be integrated with digital twins to create a 3D digital dashboard that provides a comprehensive view of all plant processes. This connectivity allows for real-time monitoring of equipment performance and environmental conditions, enabling proactive maintenance and operational adjustments.
Artificial Intelligence (AI)
Artificial intelligence can quickly analyze large volumes of data to support better decision-making. For example, AI algorithms can process machine data to predict when maintenance is needed, reducing downtime and preventing costly breakdowns. By identifying patterns in operational data, AI helps organizations optimize processes and improve overall efficiency.
Real-Time Data Analytics
Data analytics tools empower workers to make informed decisions by providing insights derived from real-time data. These tools enable employees to track performance metrics, identify trends, and assess the effectiveness of various processes. By leveraging data analytics, organizations can continuously improve operations and adapt to changing conditions in their environments.
Connected Worker Use Cases in Industrial Settings
Quality Assurance
In the realm of industrial operations, maintaining high-quality standards is crucial. Connected worker platforms empower staff by providing tools that minimize human errors throughout production processes. For example, real-time data access allows workers to quickly verify specifications and quality checks, ensuring that products meet rigorous standards before they move to the next stage of production.
Service & Maintenance
As products become increasingly complex, it is essential for service personnel to have immediate access to detailed instructions and troubleshooting guides. Connected worker platforms facilitate this by connecting workforce members with digital resources, enabling them to service customer needs effectively. For instance, technicians can use augmented reality (AR) to visualize repair processes or receive remote assistance from experts, which enhances their ability to resolve issues promptly.
Operations Management
Streamlining operations is vital for enhancing productivity levels in industrial environments. Connected worker platforms eliminate information silos by providing real-time access to plant floor data. This connectivity allows managers and workers alike to monitor operations continuously, identify bottlenecks quickly, and make informed decisions that optimize workflows. For example, location tracking of equipment can help in reallocating resources efficiently based on current operational demands.
Training & Development
With seasoned professionals retiring, capturing and transferring expert knowledge has become increasingly important. Connected worker platforms offer ongoing training opportunities through digital mentors and interactive learning modules. These tools ensure that existing employees remain knowledgeable about evolving processes and technologies. For instance, new hires can access step-by-step guides and simulations on their mobile devices, facilitating a smoother onboarding experience.
Continuous Improvement
Empowering staff with connected worker tools enables organizations to track progress toward operational goals effectively. By collecting data on performance metrics and employee feedback, companies can identify areas for improvement over time. For example, a connected worker platform might provide analytics on production efficiency or safety incidents, allowing management to implement targeted strategies for continuous improvement.
The Role of Real-Time Data in Connected Worker Platforms
Real-time data plays a crucial role in connected worker platforms, significantly enhancing operational efficiency, safety, and decision-making capabilities across various industrial sectors. By providing immediate access to relevant information, real-time data empowers workers to perform their tasks more effectively and respond promptly to changing conditions.
1. Enhanced Decision-Making
Real-time data allows connected workers to make informed decisions on the spot. For example, in manufacturing environments, workers can access live data regarding machine performance, production rates, and quality metrics. This immediate insight enables them to identify issues as they arise and take corrective actions without delay, thereby minimizing downtime and improving overall productivity.
2. Improved Safety Measures
Safety is paramount in industrial settings, and real-time data enhances worker safety by providing timely alerts about hazardous conditions. For instance, connected worker platforms can utilize geofencing technology to create virtual boundaries around dangerous areas. If a worker enters a hazardous zone, they receive instant notifications, allowing them to take necessary precautions. Additionally, features like SOS buttons and immobility detection ensure that help can be dispatched quickly in emergencies.
3. Streamlined Operations
Connected worker platforms leverage real-time data to streamline operations by facilitating better communication and collaboration among team members. Workers can share updates and insights instantly, reducing the need for time-consuming meetings or lengthy reports. For example, if a technician encounters an issue during maintenance, they can quickly connect with remote experts who can view the situation through augmented reality (AR) and provide guidance in real time.
4. Data-Driven Insights for Continuous Improvement
Real-time data collection enables organizations to track performance metrics continuously and identify trends over time. This capability is essential for continuous improvement initiatives. By analyzing data related to productivity, safety incidents, and equipment usage, companies can pinpoint areas for enhancement and implement targeted strategies to optimize processes.
5. Increased Accountability and Compliance
With real-time tracking of worker activities and equipment usage, organizations can ensure compliance with safety regulations and operational standards. For instance, location tracking systems can monitor whether workers are adhering to safety protocols by remaining within designated safe zones. This accountability fosters a culture of safety and responsibility among employees.
6. Efficient Resource Allocation
Real-time data allows for better resource management by providing insights into workforce availability and equipment status. For example, if a piece of machinery is underperforming or requires maintenance, managers can allocate resources more effectively by redirecting workers or equipment where they are needed most.
Real-time data is integral to the functionality of connected worker platforms. It enhances decision-making capabilities, improves safety measures, streamlines operations, supports continuous improvement efforts, increases accountability, and enables efficient resource allocation. By leveraging real-time information effectively, organizations can empower their workforce to achieve higher levels of productivity and safety in an increasingly complex industrial landscape.
Understanding Syook's Connected Worker Module
Syook's Connected Worker Module is designed to enhance workforce efficiency and safety by leveraging advanced digital technologies. This module addresses common challenges faced by organizations, such as low equipment utilization, worker safety concerns, and inefficiencies in operational processes. Below is an overview of its key features, benefits, and implementation strategies.
Key Features
Real-Time Location Tracking: Utilizing LoRa GPS tags and BLE beacons, the module enables precise tracking of workers and equipment across various environments, ensuring visibility and accountability.
Geofencing and Safety Alerts: The system incorporates geofencing to create virtual boundaries around hazardous areas. Workers receive immediate alerts when entering these zones, enhancing overall safety.
Emergency Response Integration: The module includes SOS buttons and immobility detection features, allowing for quick responses during emergencies. This ensures that help can be dispatched rapidly when needed.
Process Digitization: By digitizing workflows, the module reduces reliance on paper-based processes, streamlining operations and improving data accuracy.
Enhanced Collaboration Tools: The platform supports remote collaboration through augmented reality (AR), enabling experts to guide workers in real time, thereby improving task execution and troubleshooting.
Benefits
Increased Efficiency: Organizations implementing Syook's Connected Worker Module have reported significant improvements in operational efficiency, including a 75% reduction in shift changeover times.
Improved Safety Measures: Enhanced safety protocols through real-time monitoring and alerts lead to a safer working environment for employees.
Better Resource Allocation: With accurate location tracking, companies can allocate resources more effectively, ensuring that personnel and equipment are utilized optimally.
Data-Driven Insights: The module collects valuable data that can be analyzed for continuous improvement initiatives, helping organizations refine their processes over time.
Implementation Strategies
Assessment of Current Processes: Organizations should begin by evaluating existing workflows to identify areas where the connected worker module can add value.
Integration with Existing Systems: Syook's platform can be integrated with current enterprise systems to enhance functionality without disrupting established processes.
Training and Support: Providing comprehensive training for workers on how to use the connected worker tools is essential for maximizing adoption and effectiveness.
Continuous Monitoring and Feedback: Regularly assess the performance of the connected worker module to identify opportunities for further enhancement based on user feedback and operational data.
The shift toward a connected workforce represents an essential evolution in how organizations operate today. By embracing digital technologies that empower employees through seamless connectivity with people, processes, and products—companies not only enhance operational efficiency but also foster greater job satisfaction among their teams.
Syook's Connected Worker Platform stands out as an exemplary solution designed specifically for this purpose—equipping frontline workers with real-time information while facilitating collaboration across diverse teams within an organization’s ecosystem.
As businesses continue navigating their digital transformation journeys—leveraging innovative platforms like Syook will be instrumental in shaping successful outcomes that benefit both employees and enterprises alike.
Schedule a demo today and explore the benefits of connected worker solutions that transforms your frontline workforce into a digital dynamo! Experience ROI from day one! Say goodbye to dusty manuals and hello to real-time tracking, monitoring and digitization of processes at your fingertips.
Related Posts
